Improve Your Injection Molding Process with Barrel Temperature Shift Mode
ELK GROVE VILLAGE, IL, August 23, 2023 - To ensure optimal product quality, consistency, and operational efficiency, precise temperature control plays a critical role in the injection molding process. One essential feature that can significantly impact injection molding efficiency is the ability to lower and control the barrel temperature during temporary interruptions.
The V70 controller has the Barrel Temperature Shift Mode feature that lowers and controls the barrel temperature during temporary interruptions. This mode is essential for today’s modern manufacturing for several reasons.
Material Degradation Prevention
During a scheduled or unscheduled interruption in the injection molding process, the molten material inside the barrel is exposed to heat for an extended period without being injected into the mold. This can lead to material degradation, resulting in poor part quality, increased scrap, and wasted resources.
By lowering and controlling the barrel temperature during the interruption, we can minimize material degradation and maintain the material's properties. For example, if the barrel temperature is lowered to a certain temperature and held for a specific time, the polymer’s molecular structure can be maintained and its properties can be preserved.
Thermal Stability
Injection molding processes often involve precise temperature control to ensure consistent part quality and dimensional accuracy. Sudden interruptions can cause temperature fluctuations, affecting the thermal stability of the process.
By lowering the barrel temperature during the interruption, we can minimize the temperature deviation and achieve better process control. For instance, during a scheduled interruption the barrel temperature can be programmed lower to prevent the material from degrading and ensure a consistent part quality when production resumes.
Energy Efficiency
Injection molding machines consume a considerable amount of energy to maintain the barrel temperature. When an interruption occurs, it is not efficient to continue heating the barrel without any material being injected. The Barrel Temperature Shift Mode can lower the barrel temperature temporarily and helps save energy during downtime, reducing operating costs and environmental impact. For example, starting from base (room) temperature consumes more energy than a pre-programmed set point.
Equipment Longevity
Continuous exposure to high temperatures can subject the barrel and other components of the injection unit to thermal stress, which may lead to premature wear and reduced equipment lifespan.
By allowing the barrel temperature to be lowered during interruptions, we can extend the service life of the machine and its components. For example, by setting the Barrel Temperature Shift Mode to automatically lower the temperature of the barrel during idle periods, the equipment can be protected from thermal stress.
Reduced Downtime
Sometimes, interruptions in the molding process are necessary for various reasons, such as mold/machine maintenance, material changeover, or scheduled changes. With the function to lower and control the barrel temperature, the injection molding machine can resume operation more quickly and efficiently once the interruption is over.
For instance, by utilizing the shift mode program, the barrel heat-up time can be reduced, reducing downtime and increasing productivity.
Process Consistency
Consistency is crucial in injection molding to ensure that each part produced meets the desired specifications. Uncontrolled temperature changes during interruptions can lead to variations in part quality and dimensions.
By regulating the barrel temperature during the downtime, the process remains more stable, leading to consistent and repeatable results. For instance, when an injection molding machine is programmed to maintain a lower set barrel temperature during pauses in production, this can help to reduce the variance in part dimensions and material properties.
Ready to Improve Your Injection Molding Process?
In today's fast-paced manufacturing landscape, efficiency, quality, and sustainability are paramount for businesses seeking a competitive edge. To unlock the full potential of temperature control during interruptions, reach out to the Injection Molding Team to learn more about the V70 controller, equipped with the Barrel Temperature Shift Mode feature.
Tel: (888) 593-1616
Email: im-success@shibaura-machine.com
Related Articles View All Articles
Mastering Material Changeovers in Injection Molding
ELK GROVE VILLAGE, IL, August 8, 2023 - Optimizing efficiency and minimizing costs are crucial to success in the fast-paced world of injection molding. However, one aspect that often poses difficulties for molders is the purging process. The traditional me...
Read morePartnering for Success: Shibaura Machine's Technical Sales Support Services
ELK GROVE VILLAGE, IL, July 20, 2023 - As the manufacturing landscape continues to evolve, having a reliable technical sales support team becomes increasingly important. With inefficiencies in injection molding processes translating into financial losses, ...
Read moreInvest in Your Success: Shibaura Machine's Training Programs for Injection Molding Professionals
ELK GROVE VILLAGE, IL, July 5, 2023 - When it comes to injection molding, having a well-trained team is crucial for maximizing machine performance and achieving optimal results. Training ensures that all personnel understand not only the machine's capabili...
Read moreAchieving Injection Molding Excellence with Integrated Auxiliary Equipment
ELK GROVE VILLAGE, IL, June 21, 2023 - Staying ahead of the competition in manufacturing requires adopting innovative solutions that enhance productivity and efficiency. Auxiliary equipment offers a way to enable precise and automated handling of materials...
Read moreDriving Sustainable Development: The Rise of All-Electric Injection Molding Machines
ELK GROVE VILLAGE, IL, June 7, 2023 - As sustainability becomes an increasingly important focus worldwide, industries are seeking innovative solutions to align their operations with the United Nations' Sustainable Development Goals (SDGs). In the world of ...
Read moreAchieve Weight Reduction and Precise Control with Core Back Foam Molding
ELK GROVE VILLAGE, IL, May 24, 2023 - Foam molding has emerged as a highly popular and versatile technique in the plastics industry. This method offers a plethora of advantages, ranging from significant part weight reduction and improved shock absorption t...
Read moreWant to know more about our machines?
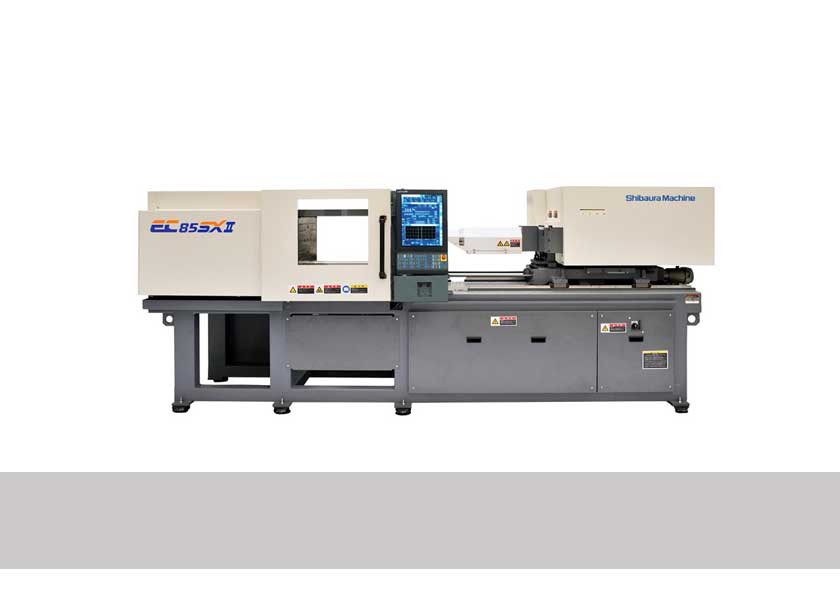
Injection Molding Machines
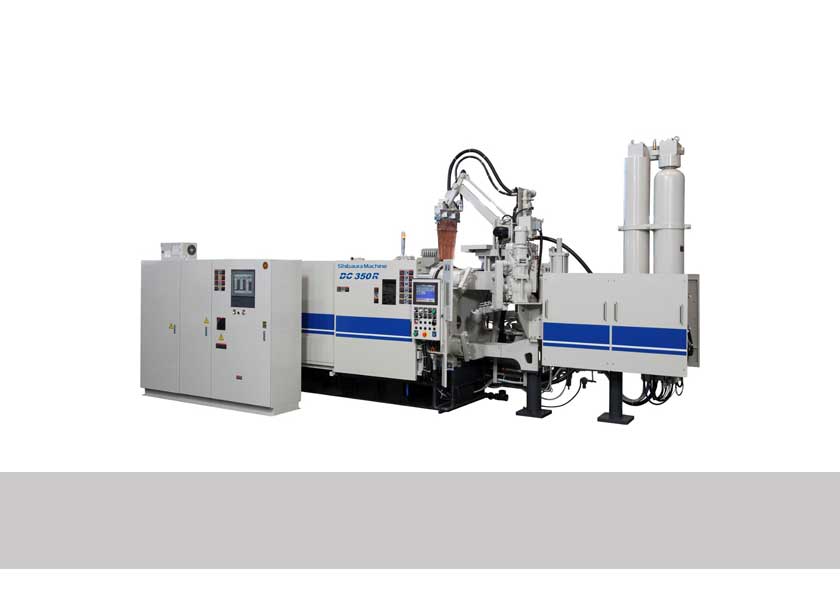
Die Casting Machines
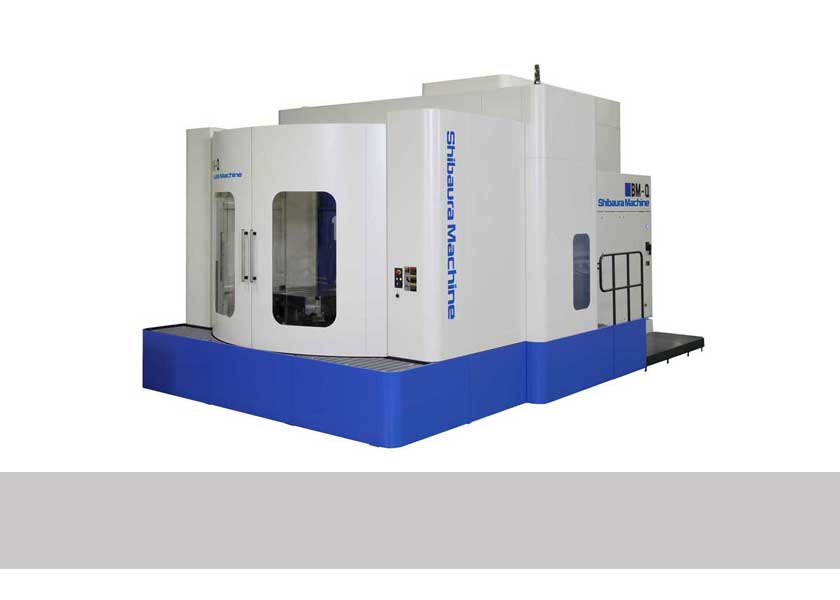
Machine Tools
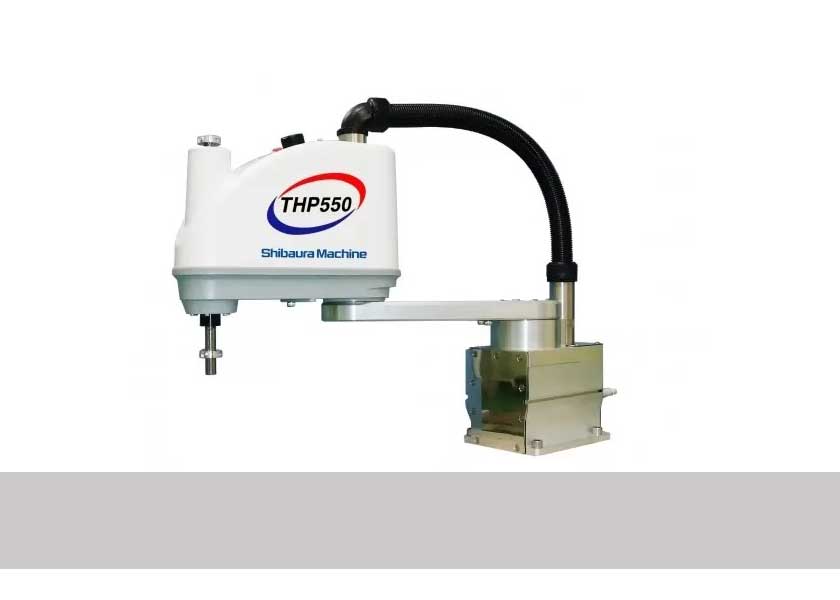